Repressing Noble Metal Ruthenium Targets to Reduce the Cost of Bipolar Plate Manufacturing in Fuel Cells
A Review: Proton Exchange Membrane Fuel Cell
The below section is directly from the United States Department of Energy website. This section explains what a PEM fuel cell is, and how it generally functions
Polymer electrolyte membrane (PEM) fuel cells—also called proton exchange membrane fuel cells—deliver high power density and offer the advantages of low weight and volume compared with other fuel cells. PEM fuel cells use a solid polymer as an electrolyte and porous carbon electrodes containing a platinum or platinum alloy catalyst. They need only hydrogen, oxygen from the air, and water to operate. They are typically fueled with pure hydrogen supplied from storage tanks or reformers.
PEM fuel cells operate at relatively low temperatures, around 80°C (176°F). Low-temperature operation allows them to start quickly (less warm-up time) and results in less wear on system components, resulting in better durability. However, it requires that a noble-metal catalyst (typically platinum) be used to separate the hydrogen’s electrons and protons, adding to system cost. The platinum catalyst is also extremely sensitive to carbon monoxide poisoning, making it necessary to employ an additional reactor to reduce carbon monoxide in the fuel gas if the hydrogen is derived from a hydrocarbon fuel. This reactor also adds cost.
PEM fuel cells are used primarily for transportation applications and some stationary applications. PEM fuel cells are particularly suitable for use in vehicle applications, such as cars, buses, and heavy-duty trucks.
Schematics of a Proton-exchange membrane fuel cells, source: Wikipedia, Marcus Eriksson, Master Thesis
The Repressing Process
A method of manufacturing noble metal sputtering targets with a spent target backer:
(a) Providing a spent target backer having a geometry and a surface that includes
a depression
(b) Placing the spent target into a graphite die designed to accommodate the geometry of the spent target backer; adding the powder to the graphite die on top of the backer plate
(c) Applying heat and uniaxial pressure in the vacuum hot-press furnace to form a high-density, high-quality target.
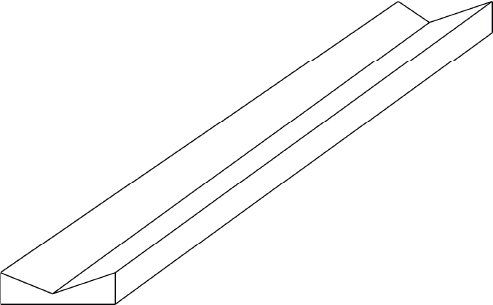
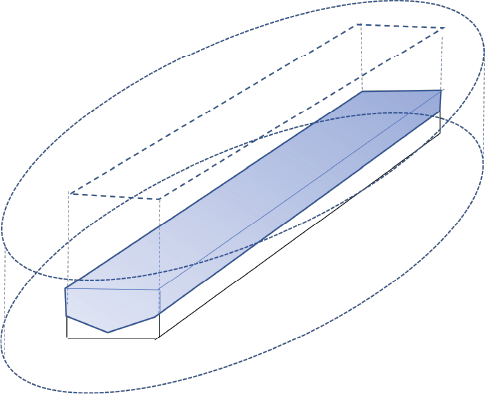
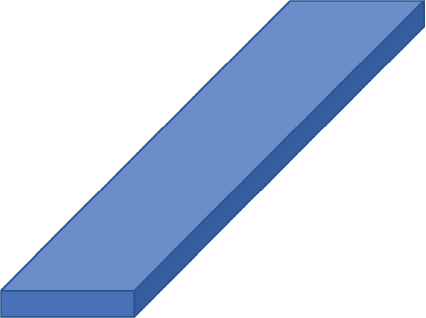
Discussion, Conclusion & References
Discussion:
The polished cross-section has no discernible interface between the virgin Ru powder & the spent target. EDAX analysis indicates no difference in chemistry between the two layer’s grains at the interface 30µm, compared with about 4µm in the bulk portion of the cross section. Repressing of Ru parts can yield a dense part with a barely discernable interface between the old and new Ru. Repressing Ru targets has the potential to reduce Ru target cost by reducing the Ru loss during refining & reducing the fees associated with refining.
Conclusion:
The repressing process is a very robust method to recycle a spent Ru target. By repressing the precious metal target, the production cost is significantly reduced due to an elongated cycle of the reclaiming unusable part of the target. Ru, Ir, and other precious metal alloys can be applied.
Contact Information:
Jing Yang, Ph.D: jyang@sciengineeredmaterials.com
Eric Massey, Sales Mgr.: emassey@sciengineeredmaterials.com